Portable Welding Equipment: The Ultimate Guide for Welders
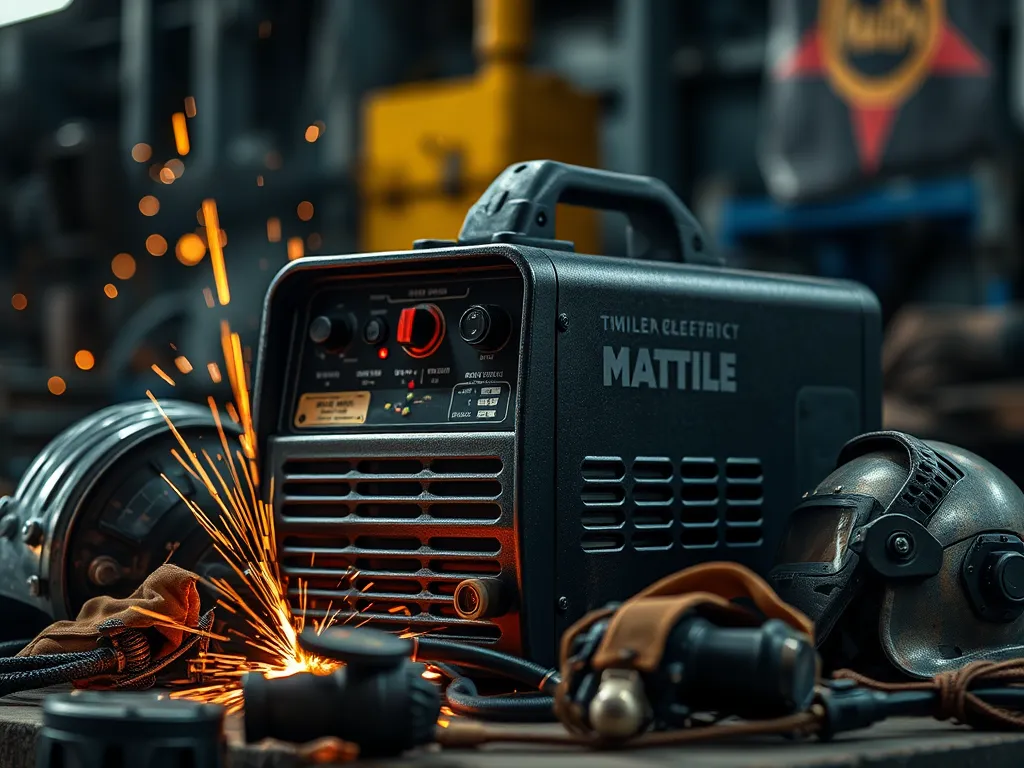
A Comprehensive Guide to Portable Welding Equipment
Portable welding equipment has revolutionized the way welding jobs are approached, providing flexibility, convenience, and efficiency in various applications. Whether used by professionals on construction sites or by hobbyists in their garages, these tools have become essential for anyone who needs to perform welding tasks without the burden of stationary setups.
On-site arc welding services provide convenient solutions for immediate repair needs.
The essence of portable welding equipment lies in its designed mobility. This equipment encompasses a wide range of welding machines that can be easily transported to different work locations. Unlike traditional welding setups that require dedicated spaces and bulky machinery, portable options allow welders to flexibly move from job site to job site while maintaining high-quality results.
Experts in Mobile TIG welding can handle even the most delicate metal works.
Various types of portable welding equipment are available, each catering to specific needs and preferences. MIG welders, known for their ease of use, are excellent for portability due to their lightweight designs. TIG welders offer precision for those who require finesse. Stick welders provide versatility for different welding materials, while battery-powered options make remote use a reality. The diversity in designs means that there is something to suit every welding application, regardless of location.
Beyond the types of machines, the benefits of portable welding equipment are numerous. They enhance productivity by enabling on-the-spot weld repairs and constructions. Welders can complete jobs more efficiently without wasting time on transporting materials to a fixed welding site. Moreover, as the equipment can be set up and dismantled quickly, the time saved contributes significantly to overall job efficiency.
In conclusion, portable welding equipment represents a significant advancement in the field of welding. Its practicality offers advantages to various users, making it a go-to choice for many. As the demand for mobility in work continues to grow, so does the importance of reliable portable welding solutions.
Types of Portable Welding Equipment
MIG welders are particularly favored for their user-friendly operation. They utilize a continuous wire feed, which makes them fast and efficient for welding thinner materials. These welders are compact, which adds to their portability, making them ideal for both professionals and DIY enthusiasts.
TIG welders are perfect for those who prioritize precision. They utilize a non-consumable tungsten electrode and a filler rod, making them excellent for welding materials like stainless steel and aluminum. Though slightly less portable than MIG welders, the latest models are designed for easy transport, ensuring they can be taken anywhere without hassle.
Portable welding methods offer flexibility and efficiency for various projects.
Stick welders are celebrated for their versatility. They can be used in a variety of environments, including windy conditions that might affect other welders. A significant advantage of stick welding is its ability to work on different material thicknesses, making it an excellent choice for diverse tasks without needing extensive setup—an appealing factor for portability.
Battery-powered welders are a game changer for remote welding applications. They allow users to weld in locations without electrical outlets, proving invaluable for outdoor or remote work. These innovative machines have become compact, yet powerful, enabling workers to tackle welding jobs in places where traditional equipment might fall short.
Benefits of Portable Welding Equipment
One of the standout benefits of portable welding equipment is the ease of transport and setup. Many models are lightweight and feature streamlined designs, ensuring that welders can quickly move their equipment from one location to another without fatigue.
The flexibility that portable welding equipment offers is unmatched. Welders can easily manage on-site projects without needing a workshop environment, allowing them to respond to jobs promptly and effectively, which is particularly beneficial in emergency situations or when working in tight schedules.
With portable welding equipment, setup time is significantly reduced. These machines can be plugged in and operational within minutes, allowing welders to begin their projects without delays commonly associated with larger, stationary welding configurations.
From a financial perspective, portable welding equipment is often cost-effective for smaller jobs. Many welders only require their equipment for occasional projects, and the ability to buy a portable unit can save them money versus investing in larger, more expensive setups that serve less frequently.
Portable Welding Equipment Maintenance
Maintaining portable welding equipment involves regular cleaning to prevent dust and debris from settling into the machines. Simple measures like wiping down surfaces and ensuring that electrical connections are free of obstructions can prolong the life of the equipment.
Battery care is crucial for the longevity of battery-powered welders. It's essential to follow the manufacturer's instructions for charging and storing batteries to avoid degradation and ensure optimal performance, especially during heavy usage periods.
An inspection checklist is also key for maintenance. Periodically checking components such as hoses, electrical connectors, and the welder's overall operational condition ensures that any potential issues are caught early, maintaining safety and functionality.
Lastly, troubleshooting common issues, such as inconsistent welding performance or equipment failure, is vital. Recognizing symptoms and knowing how to address them can save time and reduce stress during work.
Choosing the Right Portable Welding Equipment
When selecting portable welding equipment, assessing project requirements is the first step. Consider the materials you will be welding, the thickness of those materials, and the environment in which you will be working, as these factors dictate the type of welder needed.
Budget considerations are also paramount. Portable welders come in a range of prices, and understanding what you can afford while still meeting your needs is essential. Look for models that offer good performance metrics relative to their cost without compromising quality.
Weight and power factors must also be taken into account. Heavier equipment can be more difficult to transport, while lighter models may sacrifice power. Balancing these elements will ensure that you choose equipment that works for you, both in terms of weight and power availability.
Lastly, researching recommended brands and models is advisable. User reviews, expert opinions, and warranty offers can provide valuable insights and lead to better purchasing decisions based on reliability and post-purchase support.
Safety Tips for Using Portable Welding Equipment
Personal protective equipment (PPE) essentials cannot be overlooked when using portable welding equipment. Welders should invest in quality gloves, helmets, and masks to protect against sparks, UV radiation, and inhalation of fumes, ensuring their safety during operations.
Safe setup practices are crucial to prevent accidents. Ensuring that the welding area is clear of flammable materials and establishing a secure work zone can significantly minimize hazards during welding operations.
Fire prevention measures should always be in place when welding, as the process can produce sparks that ignite surrounding materials. Keeping a fire extinguisher nearby and having a plan for emergencies ensures a safer work environment.
Finally, handling hazardous materials is vital for safety. Proper storage and disposal methods for welding materials, as well as awareness of common hazards associated with specific materials, will help ensure a safe working experience.