Mastering How to Tig Weld Aluminium: A Step-by-Step Guide
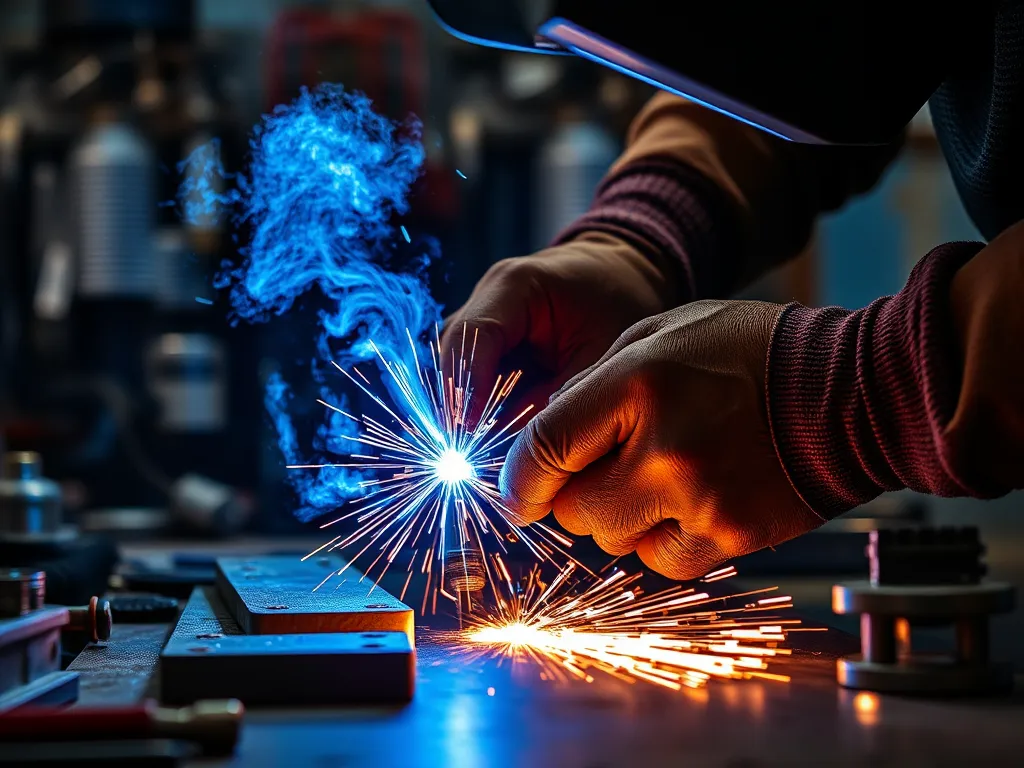
A Comprehensive Guide to TIG Welding
TIG Welding, or Tungsten Inert Gas welding, is a popular arc welding process that utilizes a non-consumable tungsten electrode to produce the weld. This method is known for its precision and versatility, making it a preferred choice in industries such as aerospace, automotive, and manufacturing. The process involves feeding a filler metal into the weld pool, while an inert gas, usually argon or helium, protects the area from contamination and oxidation during the welding process. TIG Welding is distinctive for its ability to create clean, high-quality welds with excellent control of heat input.
One of the main advantages of TIG Welding is its capability to weld a variety of materials, including stainless steel, aluminum, and magnesium. The process can be performed in all positions, which is essential for complex or vertical fabrication tasks. Unlike other forms of welding, TIG Welding does not produce slag, enabling welders to achieve smooth surfaces and precise edges. As a result, TIG Welds are often visually appealing and require minimal finishing. The technique is favored by skillful welders who appreciate the level of control it affords, allowing them to adjust settings such as amperage, travel speed, and filler metal feed.
Professionals who can tig weld aluminium are in high demand.
TIG Welding requires a range of equipment, including a TIG welder, welding torch, tungsten electrodes, and filler material. Choices of tungsten electrode types—like pure tungsten, thoriated tungsten, or ceriated tungsten—depend on the materials being welded and the desired welding characteristics. Adjusting the welding machine to the correct settings is vital for optimal performance, as factors such as material thickness and type greatly influence the parameters selected. Training and experience play crucial roles in mastering the intricate torch control and techniques required for effective TIG Welding.
As with all welding processes, safety is paramount when performing TIG Welding. Welders must wear appropriate personal protective equipment (PPE), including a welding helmet with a proper shade, protective gloves, and flame-resistant clothing. Furthermore, proper ventilation is necessary to prevent inhalation of fumes and gases released during the process. To ensure a safe workspace, it is vital to keep flammable materials away from the welding area and be aware of electrical hazards associated with operating welding equipment.
In this article, we will explore the basics of TIG Welding, specifically focusing on its application for aluminum. Aluminum poses unique challenges and considerations during the welding process, and by understanding the fundamental principles and techniques, welders can enhance their ability to produce high-quality aluminum welds. From equipment selection to post-weld finishing, our comprehensive guide aims to equip both novice and experienced welders with essential knowledge and skills related to TIG Welding.
TIG Welding Basics for Aluminium
Understanding the TIG welding process is crucial when working with aluminum. TIG Welding employs a concentrated heat source that is generated by an electric arc between a non-consumable tungsten electrode and the workpiece. In welding aluminum, the use of argon gas as a shielding agent is standard to prevent oxidation, which can weaken the weld. The skill of the welder is pivotal, as aluminum requires precise heat management to prevent burn-through or warping, which can occur due to its high thermal conductivity and low melting point.
Learning how to tig weld properly requires patience and practice.
Essential equipment for TIG welding aluminum includes a dedicated TIG welding machine, welding torch, appropriate tungsten electrodes, and a selection of aluminum filler rods. Tungsten electrodes with a sharp point are recommended for aluminum to achieve improved arc stability. Additionally, the welder should ensure that gas flow settings are optimized for aluminum, as too high or too low an argon flow can result in contamination or reduced welding quality. Proper cleaning equipment (such as stainless steel brushes) is necessary to eliminate any surface impurities prior to welding, ensuring a strong bond.
Contacting a reliable welding service is essential for complex projects.
Safety precautions for aluminum welding are similar to other welding processes but have additional considerations due to unique challenges associated with aluminum materials. Adequate ventilation is paramount to remove harmful fumes that can develop during the welding process. Furthermore, aluminum emits bright reflections, so it is essential to use auto-darkening helmets to protect the eyes. Additionally, protective gloves and clothing are necessary to prevent skin burns from heat radiation or spatter.
Techniques for TIG Welding Aluminium
Holding the torch correctly while welding is vital for creating quality aluminum welds. The welder should maintain a steady hand while positioning the torch at an angle of about 10-15 degrees to the workpiece. A proper grip allows for enhanced control over the welding process and helps to maintain an even arc length. The welder should ideally use a triangular torch motion to increase the stability and consistency of the weld pool, ensuring smooth transitions.
Controlling the heat for aluminum is critical due to its tendency to warp or melt quickly under excessive heat. TIG welders should adjust their amperage settings according to the thickness of the aluminum and utilize a pulsed TIG welding technique if necessary. Pulse welding allows for managing the heat input more effectively, resulting in lower overall heat stress on the material. Frequent pauses in the welding arc can also assist in dissipating heat and maintaining control.
Creating strong and clean welds is achievable through practice and focus on technique. Using the correct filler metal, such as 4047 or 5356 aluminum alloy, can enhance weld strength and compatibility. Maintaining a clean welding environment by ensuring the surfaces are free from dirt, grease, and oxide layers promotes strong metallurgical bonding. Experienced TIG welders often develop a rhythmic pattern in their welding, and integrating this with optimal settings helps to deliver high-quality results.
Common Challenges in Aluminium TIG Welding
Dealing with oxidation on aluminum surfaces is one of the primary challenges faced in TIG welding. Aluminum readily oxidizes, and the oxide layer must be removed to achieve proper fusion. Welders should consider using a stainless steel brush or chemical cleaning methods to prepare the weld area adequately. Failure to address oxidation may lead to poor weld strength and integrity, often resulting in defects such as porosity.
Avoiding warping during the welding process is critical, particularly when working with thin aluminum sheets. Welders can minimize warpage by employing techniques such as tacking the pieces together strategically, working from the center towards the edges, or using cooling methods between passes. It is beneficial to maintain consistent heat levels across the weld or utilize a backstepping technique to control heat distribution effectively.
To prevent contamination in TIG welding, maintaining a clean working environment is essential. This includes ensuring that the torch and tungsten electrode are clean and free from debris or contaminants that can adversely affect the weld quality. Additionally, controlling the gas flow and checking for leaks in the gas supply lines can help maintain the inert environment necessary for a successful aluminum weld.
Advanced TIG Welding Techniques for Aluminium
Multi-pass welding for thicker aluminum materials involves making multiple passes to achieve the desired penetration and weld profile. Welders should oscillate the torch in a pattern that effectively fuses the aluminum during each pass while allowing for cooling between passes. This technique enables welders to distribute heat more evenly, ultimately resulting in stronger constructions without compromising the material's integrity.
Using fillers and their appropriate types is essential for achieving optimal welding results in aluminum TIG welding. Various filler materials are available, such as ER4047 for a lower melting point or ER5356 for higher strength. The chosen filler rod should complement the base material's properties to ensure good fusion and mechanical strength of the final weld. Selecting the correct filler will also help reduce the risk of cracking and enhance overall weld quality.
Welding in different positions and angles presents unique challenges in aluminum welding. Experienced welders can adapt their technique to accommodate overhead, vertical, or horizontal positions through adjustments in torch angle and travel speed. Understanding the physics of molten aluminum helps welders anticipate the tendencies of the weld puddle in different orientations, which ultimately influences their overall technique and success in various welding scenarios.
Post-Weld Cleanup and Finishing for Aluminium
Removing slag and cleaning welds is an integral part of post-weld cleanup after TIG welding aluminum. While TIG Welding produces minimal slag compared to other processes, any residual contaminants should be removed thoroughly using appropriate cleaning tools. Acidic solutions or mild abrasives may be employed, but care should be taken to avoid damaging the aluminum surface during the cleaning process.
Polishing and finishing welded aluminum parts significantly enhance the aesthetic and functional qualities of the welds. Common methods such as mechanical polishing, bead blasting, or chemical treatments can be used to achieve a desired surface finish. Each of these techniques offers a different result, and the choice largely depends on the intended application of the aluminum components.
Preventing corrosion on welded areas is essential for ensuring longevity and durability. Post-weld treatments, such as anodizing or applying protective coatings, can effectively shield the aluminum from environmental elements. Additionally, proper storage and handling techniques should be enforced to protect welded pieces from exposure to moisture and humidity, thereby preventing the onset of corrosion.