Essential Safety Practices for Arc Welding Operations
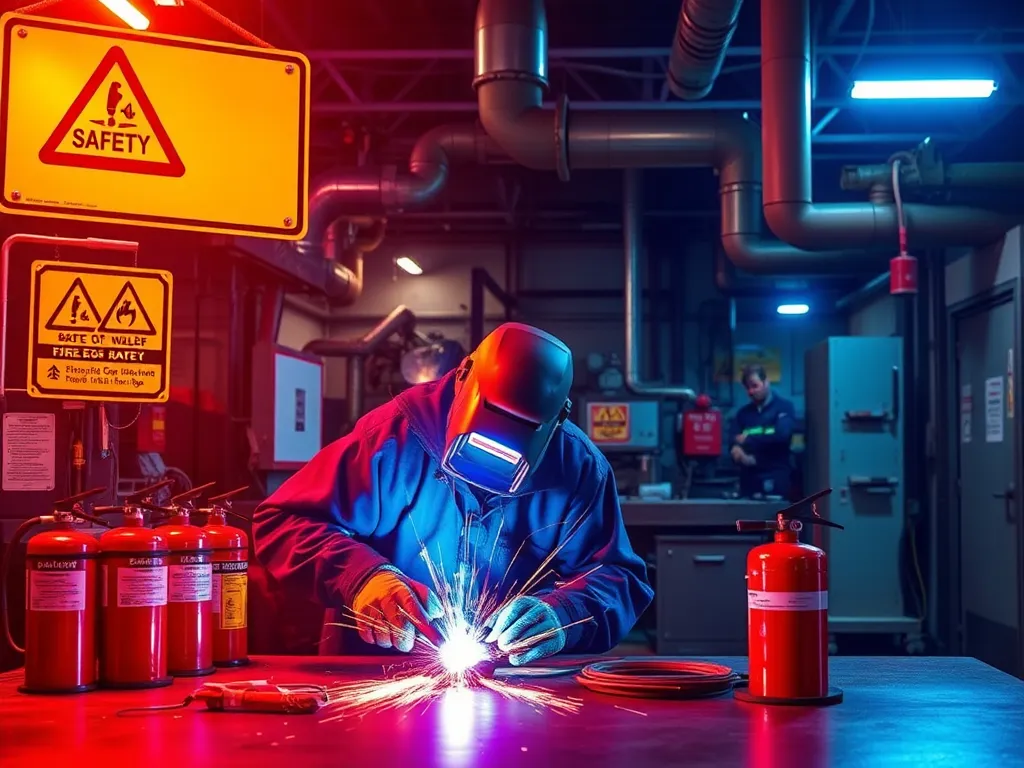
Safety Practices for Arc Welding Operations
Arc welding is a widely used metal joining process, but it comes with numerous risks. Practicing safety in arc welding operations is essential to protect workers from injuries and health hazards. Implementing robust safety practices not only ensures the well-being of welders but also enhances productivity and efficiency. This article outlines critical safety practices for arc welding operations, emphasizing the importance of preparation, proper equipment, and awareness of environmental factors.
Utilizing appropriate welding PPE is essential to protect welders from harmful sparks and heat.
To uphold safety in arc welding operations, a comprehensive understanding of common hazards associated with welding is vital. These include exposure to harmful fumes, risks of burns, and potential electric shocks. Furthermore, corrosive materials present in welding processes can lead to skin exposure and toxicity. Therefore, being aware of hazards and adopting necessary safety measures is an integral part of effective welding operations that help mitigate risks and safeguard worker health.
To implement optimal Safety Practices for Arc Welding Operations, employers must prioritize the training of employees. Educating welders on proper techniques and operational standards fosters a culture of safety that can prevent accidents. Regular safety meetings and training sessions covering updates on safety practices reinforce the importance of maintaining a safe working environment. Furthermore, competence assessments help identify areas requiring additional training and monitoring to ensure that all welders are sufficiently prepared to handle potential risks in their work.
Implementing strict electrical safety precautions can significantly reduce the risk of accidents in welding operations.
Using the correct Personal Protective Equipment (PPE) is an indispensable component of welding safety. An effective PPE program involves wearing appropriate protective clothing, helmets, gloves, and footwear to reduce the chances of serious injury. In addition to personal gear, providing well-maintained tools and equipment is necessary to achieve safety in arc welding operations. Keeping tools in optimum condition reduces the risk of accidents due to faulty or broken equipment.
Understanding the ventilation requirements in welding areas helps ensure a safe and healthy workspace.
Lastly, incident reporting is crucial for creating a safety-conscious workplace. Establishing a system where employees can report unsafe conditions, incidents, and near misses without fear of reprisal fosters an environment of communication and awareness. Analyzing reports can lead to identifying patterns, allowing for the improvement of safety measures and techniques in arc welding operations.
Personal Protective Equipment (PPE) for Welding Safety
Personal Protective Equipment (PPE) forms the first line of defense in welding operations. For arc welding, essential types of PPE include welding helmets with appropriate shading levels to protect against UV radiation, gloves made of leather or other flame-resistant materials, and flame-retardant clothing. Workers should always wear the correct gear specific to the type of welding they are performing to ensure maximum protection.
The importance of wearing protective clothing cannot be overstated. Welding can produce sparks, hot molten metal, and UV radiation, all of which can cause severe burns and injuries without proper clothing. Therefore, wearing flame-resistant clothing, such as jackets, gloves, and aprons, provides a critical barrier that helps guard against these dangers. Adopting a ‘no bare skin’ policy ensures that the risk of injury from sparks and heat is minimized.
Proper eye protection is essential for welders. When performing arc welding, welders should use helmets with auto-darkening lenses or goggles that provide adequate shielding against bright light and harmful rays. This not only protects against temporary vision damage but also long-term eye health concerns. Ensuring that eye protection is worn at all times while welding significantly reduces the risk of visual impairment.
Footwear safety standards for welding include wearing steel-toe boots that protect from falling objects and are slip-resistant. Additionally, boots should be made of fire-resistant materials to prevent burns when sparks come into contact. Implementing strict footwear regulations in the workplace ensures that welders have the proper protection against risks associated with their operational environments.
Using gloves specifically designed for welding work is another crucial safety practice. High-quality leather gloves insulated against heat prevent burns and cuts during operations. Welders should also ensure that gloves fit properly, enabling them to maintain dexterity while handling tools and materials. Investing in quality gloves significantly contributes to minimizing injuries during welding tasks.
Welding Environment Safety Standards
Ventilation is critical in welding areas to ensure the safety of workers. Proper air circulation helps disperse harmful fumes and gases produced during welding, reducing the risk of respiratory issues. Employers should assess welding locations to ensure adequate ventilation systems are in place and operational. Using fume extraction systems or ensuring open spaces during welding can significantly improve air quality.
Setting up a safe welding workspace is essential for minimizing accidents. This includes clearing the area of clutter and creating designated zones for welding activities. Proper storage for materials, equipment, and flammable items should also be maintained. A clean and organized environment helps welders stay focused and minimizes the likelihood of tripping or making errors during operations.
Keeping flammable materials away from welding zones is vital. A safety perimeter should be established to create buffer zones free from flammable substances, which can ignite from sparks or heat generated during welding. Providing adequate signage and training workers on the dangers of fire hazards reinforces the importance of maintaining safety measures in welding operations.
Temperature control during welding is an often-overlooked safety aspect. High temperatures can lead to equipment malfunction or damage and increase the risk of burns. Ensuring that welding processes stay within safe limits and that equipment is appropriately rated for temperature thresholds is crucial to preventing accidents and injuries in the workspace.
Ergonomics in welding positions is essential for the long-term health and well-being of welders. Workers are encouraged to use adjustable equipment and tools that enable them to maintain proper posture while welding. Implementing ergonomic practices reduces the risk of musculoskeletal disorders and enhances overall comfort during operations, helping maintain productivity and safety.
Emergency Preparedness in Welding Operations
Creating an emergency response plan tailored to welding operations is essential. Such a plan should outline standard operating procedures for fires, accidents, or injuries that may occur. Emergency contacts, reporting procedures, and clear evacuation routes must be established so that workers know exactly what to do in case of an emergency situation.
Training for welding emergencies is necessary to ensure that all personnel are prepared to respond quickly and effectively. Regular drills and training sessions should cover different types of emergencies that could arise during welding operations. Workers should be familiar with how to use fire extinguishers, first aid kits, and emergency exit routes to foster a culture of preparedness.
First aid kits in welding operations must be adequately stocked and easily accessible to ensure rapid response to injuries. Having the necessary supplies like bandages, antiseptics, and burn treatments enhances the ability to manage minor injuries and ailments. Additionally, training personnel on how to utilize first aid kits effectively is crucial to ensuring safety during emergencies.
Understanding different types of fire extinguishers and their appropriate uses is essential for welding operations. Training workers on how to choose the correct extinguisher for the type of fire they may encounter prevents situations from escalating. Regularly checking and maintaining fire extinguishers ensures they remain functional and ready for use in emergencies.
Reporting incidents and near misses is a vital component of welding safety. Encouraging a culture where workers share concerns and report unsafe or dangerous conditions contributes to the overall enhancement of safety practices. Analyzing reports helps management identify problem areas and implement necessary changes that could further minimize risks in welding operations.
Health Risks and Mitigation Strategies
Identifying respiratory risks in welding is crucial for ensuring worker health. Exposures to toxic fumes and gases can lead to long-term health effects, including respiratory illnesses. Implementing regular air quality assessments and ensuring the use of respiratory protection when necessary helps control exposure to harmful elements during welding.
Preventing skin burns and injuries in welding is vital, as welders are exposed to intense heat and molten metal. Proper protective clothing and equipment serve as the first line of defense against thermal injuries. Additionally, employing safe handling techniques can help reduce the risk of accidents that lead to burns.
Dealing with eye exposure to light during welding is critical. The intense light produced can lead to conditions like 'arc eye'. Thus, using appropriate protective gear and ensuring shields are in place contribute to minimizing exposure. Regular eye checks for welders help maintain long-term visual health.
Noise exposure is another critical concern in weld welding operations. Prolonged exposure to high decibel levels can lead to hearing loss. Implementing hearing protection like earplugs or earmuffs, along with regular hearing assessments, protects workers from noise-induced conditions linking back to health risks.
Understanding the long-term health effects of welding fumes is essential, as continuous exposure can result in chronic conditions. Employers must ensure that proper ventilation is in place and that mitigation strategies are implemented to limit inhalation of harmful substances. Regular health monitoring for welders can help identify early indicators of health deterioration due to welding fumes.
Training and Certification for Welders
The importance of safety training for welders cannot be overlooked. Effective training programs equip welders with the knowledge and skills to practice safety measures diligently. Integrating safety protocols into regular training ensures that welders are aware of the latest developments in safety practices and are prepared to implement them during operations.
Certification programs for welding safety are essential as they provide formal acknowledgment of a welder's competency in safe practices. Ensuring that welders maintain certification and participate in refresher courses enhances workplace safety significantly. Employers should encourage welders to pursue certification to promote a culture of safety and excellence in welding operations.
Continuous education on new safety practices is crucial for keeping welders informed about industry updates and innovations. Employers should invest in ongoing training sessions, seminars, and workshops that focus on the latest safety practices and technologies. Keeping welders educated fosters an environment of continuous improvement in safety practices.
Hands-on training for emergency scenarios reinforces welders' readiness to respond to incidents. Conducting simulations and drills helps workers practice appropriate responses to various emergency situations. This not only increases confidence but also ensures that welders can act quickly and effectively when faced with real emergencies.
Evaluating welders’ safety competency through regular assessments is necessary for maintaining safety standards in welding operations. Employers should conduct evaluations to gauge understanding and compliance with safety protocols. Continuous monitoring helps identify areas of improvement and encourages welders to stay vigilant about their safety practices.