Discovering the Strongest Welding Types for Your Projects
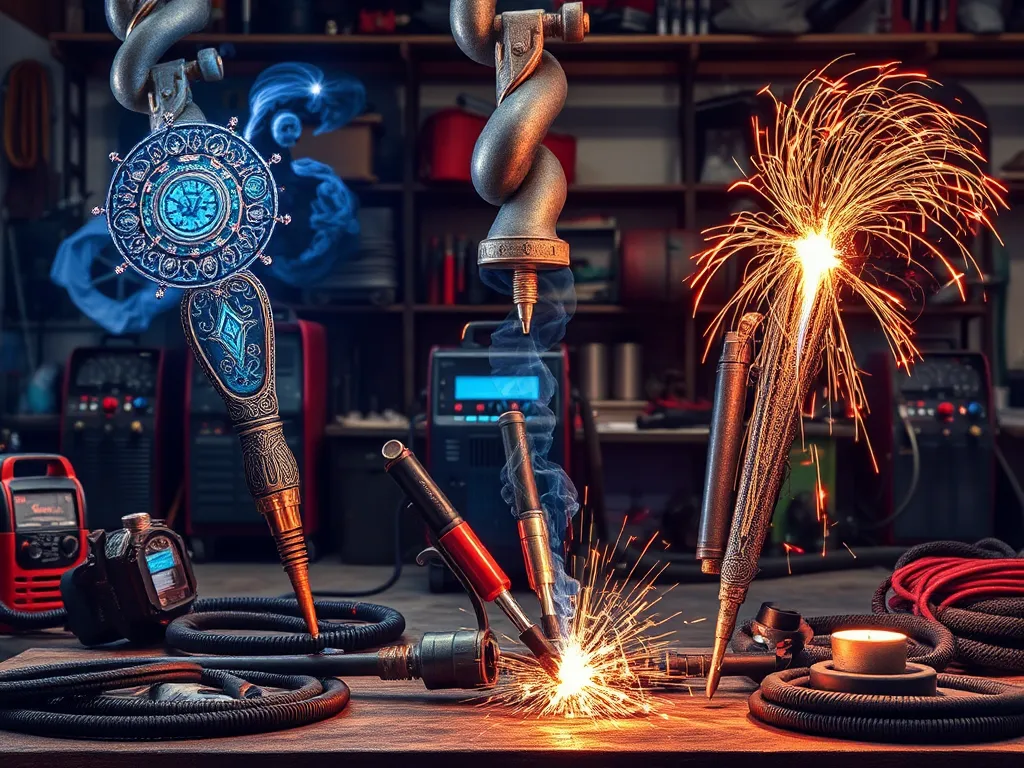
Welding Techniques: A Comprehensive Guide
Welding Techniques are essential methods used in metal joining processes to create strong and durable connections. These techniques have evolved over the years, allowing for a variety of applications across different industries. Mastering these techniques can significantly enhance the efficiency and effectiveness of metalworking projects, leading to superior results that meet specific engineering requirements.
Among the various Welding Techniques, some of the most common include MIG, TIG, Stick, and Flux-Cored Arc Welding. Each of these methods has unique characteristics that make them suitable for different tasks. Knowing when and how to apply these techniques is crucial for any welder seeking to optimize their work and achieve the desired weld quality.
One of the critical aspects of Welding Techniques is the ability to assess and compare the strength of welded joints. This involves understanding the types of metals being used, the welding processes, and the environmental factors that may affect the final outcome. A strong weld is not just about the technique itself but also about knowing how to manipulate the materials and conditions.
One of the most critical factors in ensuring the durability and reliability of welded structures is selecting the appropriate high-strength weld types, which are essential for projects requiring exceptional load-bearing capacity and resistance to stress.
Additionally, the application of strong welds is vast, ranging from construction and automotive industries to aerospace and maritime uses. Each industry demands specific requirements and standards for weld strength, making it essential for welders to adapt their techniques accordingly. Understanding the applications will help welders appreciate the importance of mastering various welding methods.
In summary, Welding Techniques encompass a broad spectrum of processes and knowledge that practitioners must acquire to excel in the trade. Continuous learning and practice are critical as technology advances and new materials emerge, requiring designers and welders to innovate their techniques to achieve robust and reliable welded joints.
When working on different welding techniques, it's important to consider how material thickness, joint design, and environmental conditions can impact the overall durability of the weld. Welding strength factors play a crucial role in ensuring the structural integrity of your project, regardless of the specific technique used.
Types of Welding
MIG Welding, or Metal Inert Gas welding, is one of the most popular welding techniques. It employs a continuous wire feed as an electrode and uses an inert gas to protect the weld area from contamination. MIG welding is known for its speed and ease of use, making it ideal for both beginners and experienced welders alike. It is commonly used in automotive and manufacturing applications due to its versatility.
TIG Welding, or Tungsten Inert Gas welding, is another widely used technique that produces high-quality welds. It utilizes a non-consumable tungsten electrode and an inert gas to shield the weld area. While TIG welding requires more skill and experience, the precision it offers makes it a favorite for applications demanding clean and strong joints, such as aerospace and pipe welding.
In exploring the various strongest welding techniques, it becomes clear that mastering these methods can significantly enhance the quality and durability of your projects.
Stick Welding, or Shielded Metal Arc Welding (SMAW), is one of the oldest welding techniques, using a consumable electrode coated in flux. When the electrode melts, it creates a shielding gas that protects the weld. Stick welding is versatile and can be used in various positions, making it suitable for outdoor and heavy-duty applications, such as construction and shipbuilding.
Flux-Cored Arc Welding (FCAW) is similar to MIG welding but uses a tubular wire filled with flux instead of solid wire. This allows for deeper penetration and makes it suitable for thicker materials. FCAW can be performed with or without shielding gas, which adds to its versatility in various environments, including outdoor conditions.
Submerged Arc Welding (SAW) involves the formation of an arc between a continuously fed electrode and the workpiece, with the weld area being submerged under a blanket of granular flux. This technique provides high penetration and is often used for heavy fabrication, such as steelwork in shipbuilding and pressure vessels.
Strength Comparisons
When it comes to Welded Joint Strength, the type of metal used significantly influences the final strength of the weld. Different metals possess varying characteristics, including tensile strength, ductility, and workability. Understanding these properties helps in selecting the appropriate welding technique and material combination for specific applications.
The Comparison of Welded Joint Strength involves evaluating the quality and durability of different welding processes. Some techniques yield stronger welds than others, effectively determining their best applications. For instance, MIG welding provides efficient production speed but may not achieve the same strength levels as TIG welding in critical applications.
Several Factors Affecting Weld Strength include material type, welding technique, and environmental conditions during the welding process. Variables such as temperature, humidity, and even the skill of the welder can lead to variations in weld quality and strength. Awareness of these factors is essential for achieving the desired weld integrity.
Welding Process Strength Ratings give an indication of the reliability and quality of a weld produced by a specific technique. Different welding processes have standardized ratings that help engineers and welders evaluate the suitability of a welding method for a given application. Understanding these ratings assists in making informed decisions during the design and fabrication stages.
Testing Methods for Weld Strength are employed to ensure that the welded joints meet the specified strength criteria. Common testing methods include tensile tests, bend tests, and impact tests, which assess the performance of the weld under different conditions. These tests are crucial for maintaining the safety and reliability of welded structures.
Applications of Strong Welds
Construction and Structural Welding rely heavily on strong welds to create safe and durable structures. High-strength welded joints are vital for load-bearing components, ensuring that buildings and bridges can withstand various stresses and environmental factors. The construction industry prioritizes rigorous welding standards to comply with safety regulations.
The Automotive Industry Welding is another area where strong welds are essential. Vehicles undergo rigorous testing for durability and safety, which places significant demands on the welds used in their construction. Manufacturers often use advanced welding techniques to ensure the structural integrity of critical components like chassis and frames.
Aerospace Welding Requirements are stringent due to the high safety standards mandated in the industry. Welds used in aerospace applications must withstand extreme conditions, including high speeds, temperature variations, and stress during flight. As a result, techniques like TIG welding are often employed for their precision and strength in critical components.
Marine Applications of Strong Welds are vital for constructing ships and offshore structures that face harsh marine environments. Strong welds are necessary to ensure the strength and durability of vessels, which encounter constant wave and wind forces. Reliable welding techniques and materials are critical to preventing catastrophic failures.
Artistic and Decorative Welding Uses showcase the versatility of strong welds beyond traditional applications. Artists and designers often use innovative welding methods to create sculptures, railings, and other decorative elements. In these scenarios, the quality and aesthetics of the welds play a significant role in the final product.
Best Practices for Strong Welds
Preparing Base Metals for Welding is a crucial step to ensure strong welds. Proper surface cleaning, alignment, and fitting of the materials can significantly improve the bond quality. Addressing rust, paint, and impurities before welding can help avoid common defects and enhance weld strength.
Choosing the Right Filler Material is essential for achieving a strong weld. Different materials and compositions have unique properties that should match those of the base metal being welded. Using the appropriate filler can enhance the strength, durability, and corrosion resistance of the weld joint.
Welding Techniques for Maximum Strength involve selecting the proper parameters, such as voltage, amperage, travel speed, and torch angle. Adjusting these parameters to reflect the specific joint design and material characteristics leads to higher quality and stronger welds.
Post-Weld Treatments for Strength include processes like heat treatment, machining, and surface finishing, which can improve the overall integrity and performance of the weld. Implementing these treatments helps relieve residual stresses and enhances the mechanical properties of the welded joint.
Inspection Techniques for Strong Welds ensure that the welded joints meet the quality standards required for safety and performance. Techniques such as visual inspection, ultrasonic testing, and X-ray inspection are used to evaluate weld quality and detect potential defects before they lead to failures.
Welding Equipment and Tools
Best Welding Machines for Strength are specifically designed to accommodate various welding techniques and materials. When selecting a welding machine, it’s crucial to consider the machine's power output, compatibility with welding processes, and the type of material being worked on to achieve optimal results.
Choosing the Right Welding Consumables, including electrodes, filler wires, and gases, is essential for ensuring the quality and strength of the weld. Understanding the specific requirements of each welding process allows welders to select the appropriate consumables for their projects effectively.
Safety Gear for Strong Welding is a non-negotiable aspect of the welding process. Welders must wear appropriate personal protective equipment (PPE), including helmets, gloves, and flame-resistant clothing, to protect against hazards associated with high temperatures, sparks, and harmful fumes.
Maintenance of Welding Equipment is essential for optimal performance and longevity. Regular inspections, cleaning, and component replacement help ensure that welding machines and tools operate effectively, contributing to the production of strong, reliable welds.
Innovative Tools for Better Weld Strength have emerged with advancements in technology, improving the welding process's efficiency and results. From automated welding machines to advanced monitoring systems, these tools provide welders with enhanced capabilities to produce stronger and more precise welds.