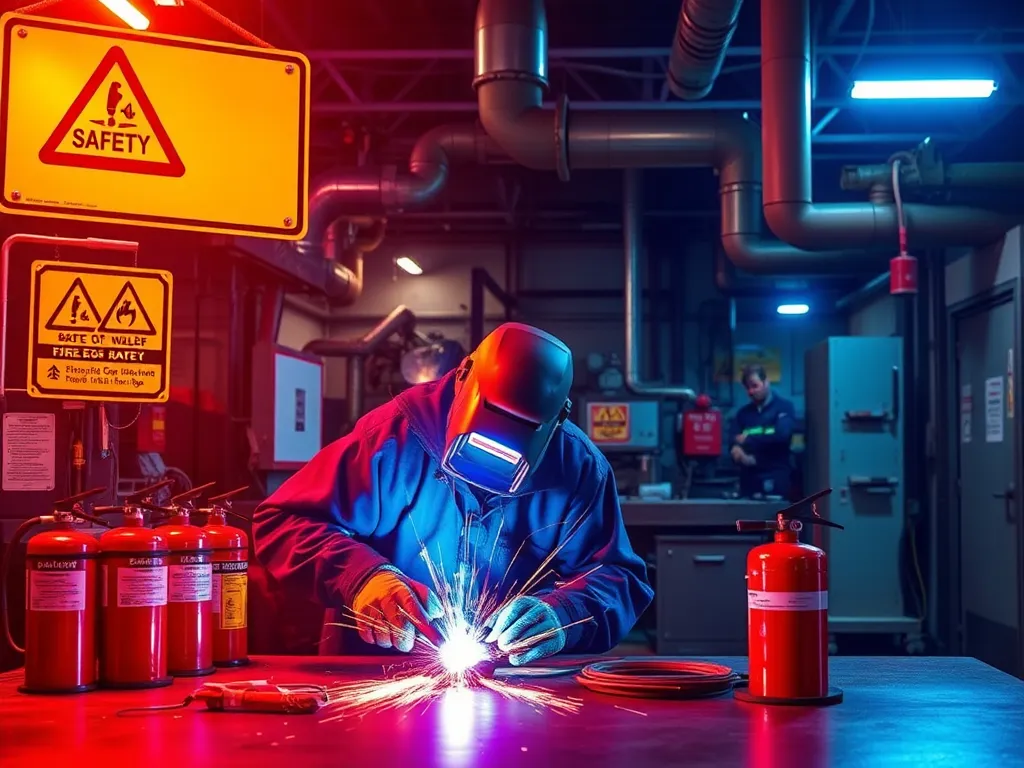
Best Practices for Operating Welding Machines on Job Sites for Safety and Efficiency
Key Takeaways
- Comprehending Welding Equipment
- Optimal Techniques for Utilizing Welding Machines in Work Environments
- Necessary Welding Equipment for Work Locations
- Safety Guidelines in Welding Activities
- Ecological Factors in Welding Practices
Understanding Welding Machines
Welding machines come in various types, each designed for specific tasks and materials, such as MIG welding, stud welding, or using welding rods. Understanding these machines is essential for welders aiming to improve their skills and ensure high-quality results. The American Welding Society (AWS) provides guidelines that emphasize the importance of mastering these machines for safety and effectiveness. Best Practices for Operating Welding Machines on Job Sites play a critical role in minimizing risks associated with welding fumes and ensuring that essential safety gear, like welding helmets, is properly utilized. Each machine and technique has unique characteristics, making proficiency in their operation vital for successful welding outcomes.
Types of Welding Machines Used on Job Sites
Different types of welding machines are commonly used on job sites, each suited for specific applications. Arc welders, for example, utilize an electric welding arc to create high-temperature welds. Carbon-arc welding is another popular method, where a carbon electrode produces a high-intensity arc that melts the base metal. These machines are essential for various hot work tasks, and understanding their capabilities is critical for achieving strong, durable welded joints.
A welder must be proficient in operating these machines to ensure quality and safety. The sparks generated during the welding arc can pose risks, making it vital to follow Best Practices for Operating Welding Machines on Job Sites. Proper machine setup and technique play a significant role in the quality of the weld. Ensuring that machines are maintained and inspected regularly leads to fewer incidents and improved efficiency in creating robust welds on-site.
- Understanding the different types of welding machines helps select the right one for each task.
- Regular maintenance of welding machines reduces downtime and improves performance.
- Properly trained welders increase safety and minimize the risk of workplace accidents.
- Familiarity with the equipment's specifications aids in optimizing settings for various materials.
- Following safety protocols protects both the welder and surrounding personnel.
- Ensuring that the job site is clean and organized can prevent accidents related to equipment use.
- Investing in quality machines can lead to more efficient and effective welding practices.
Safety Features of Modern Welding Equipment
Modern welding equipment integrates advanced safety features to enhance occupational safety and health practices. This includes the use of exhaust hoods that effectively manage fumes and improve air quality on job sites. Contractors benefit from these tools as they not only help in maintaining compliance with Occupational Safety and Health Administration standards but also reduce long-term maintenance costs associated with health-related issues. Proper ventilation is crucial, especially in environments where metal and structural steel are being processed.
Welding machines are designed with multiple protective elements to safeguard operators. Features such as automatic shutdown systems and overload protection minimize the risk of accidents, aligning with the Best Practices for Operating Welding Machines on Job Sites. Personal protective equipment (PPE) is often supplemented by these safety mechanisms, offering welders additional layers of protection against hazards. As manufacturing and construction practices evolve, the integration of these safety features continues to improve overall well-being in the workplace.
Best Practices for Operating Welding Machines on Job Sites
Adhering to Best Practices for Operating Welding Machines on Job Sites is essential for ensuring both safety and efficiency. The Occupational Safety and Health Act mandates that welders employ personal protective equipment (PPE) such as safety glasses and gloves to prevent injuries. Utilizing power tools designed to meet Underwriters Laboratories (UL) standards guarantees reliability. It is crucial for steel erectors to implement technologies like proper exhaust systems to manage fumes and maintain air quality on the jobsite. Ensuring that the welding equipment’s engine operates correctly can lead to more consistent results. By following these guidelines, workers can cultivate a safe environment and enhance productivity through the integration of advanced technology.
Pre-Operation Inspections and Maintenance
Regular inspections and maintenance are vital for ensuring optimal performance from welding machines and equipment. Implementing best practices for operating welding machines on job sites begins with a thorough check of all components, including cables, hoses, and connections. Proper cable management can prevent accidents and enhance safety, reducing the risk of flame hazards. A clean and organized welding area not only promotes efficient welding processes but also contributes to a safer welding environment, minimizing distractions.
Before commencing any welding operation, operators should verify the condition of personal protective equipment (PPE) and ensure that all safety features are functioning correctly. Following the best practices for operating welding machines on job sites helps to identify potential issues before they escalate. A proactive approach to maintenance can lead to more productive welding processes, ultimately improving the overall reliability of equipment within the welding industry. Prioritizing these checks fosters an environment conducive to optimal welding performance.
Proper Setup and Positioning of Welding Equipment
Correct setup and positioning of welding equipment is crucial for optimal performance and safety during current welding operations. Implementing best practices for operating welding machines on job sites includes evaluating the specific needs of certain welding situations. Properly arranging the workspace and ensuring that welding gear is accessible contributes to welding efficiency. Utilizing electric welding safety protocols and ensuring that the equipment is stable will enhance steady welding, allowing for precise execution of welding processes.
Attention to detail in setup can significantly influence outcomes, particularly in challenging environments. Ensuring that all welding gear, such as welding gloves and safety equipment, is within reach can prevent delays and promote safe welding practices. Adhering to stud welding safety measures also plays a critical role in effective positioning. Understanding the nuances of various welding applications allows welders to maximize their performance and maintain safety standards, creating a productive and safe working atmosphere.
Essential Welding Gear for Job Sites
Proper gear is crucial for welders, ensuring safety and enhancing performance during operations. Skilled welders in Xpress Mobile Welding Phoenix, whether engaged in stud welding operations or wire welding, must equip themselves with Personal Protective Equipment (PPE) that meets the standards set by the American Welding Society. Experienced welders know that frequent welding parameters can vary across different tasks, so having the right tools and accessories is essential for successful welds. Portable welders often rely on high-quality gear to maintain efficiency on job sites. Following best practices for operating welding machines not only contributes to safety but also fosters a professional environment where good welders can thrive. This focus on gear and safety helps area welders attain the level of expertise required in the stud welding industry.
Personal Protective Equipment (PPE) for Welders
Welders require specific protective gear to ensure safety while operating welding machines on job sites. Structural welders, flux core welding technicians, and voltage welding operators must invest in high-quality helmets with appropriate filters to protect their eyes from intense light and harmful radiation. Quality welds depend not only on skill but also on the right equipment. Welders-in-training must be equipped with gloves that resist heat and sparks, along with flame-resistant clothing to prevent burns.
The implementation of best practices for operating welding machines on job sites often involves wearing the correct personal protective equipment. Engine-driven welders need to be conscious of their surroundings to avoid trips and falls. Employing a comprehensive weld procedure ensures that high weld quality is maintained, highlighting the importance of proper gear. Invest in quality PPE to safeguard against the hazards of welding while consistently achieving high-quality welds.
Contact Xpress mobile welding for any custom metal fabrication work needed. The offer a mobile welding service in the Phoenix AZ and surrounding area.
- Choose helmets with auto-darkening filters for enhanced convenience and safety.
- Use heat-resistant gloves that provide ample dexterity for handling welding materials.
- Wear flame-resistant clothing, such as jackets and pants, to protect against sparks and heat.
- Equip yourself with safety boots that offer steel toes and slip-resistant soles for added protection.
- Incorporate face shields alongside helmets for additional facial protection from sparks and debris.
- Regularly inspect and maintain PPE to ensure it remains in good condition and effective.
- Attend training sessions on proper PPE usage to maximize safety and compliance on the job.
Additional Tools and Accessories for Efficient Welding
Efficient welding operations often depend on the right tools and accessories alongside the primary welding machine. An engine-driven welder can offer flexibility and portability, especially for outdoor job sites. Keeping quality weld cables in good condition is crucial, as worn cables can lead to weld quality issues and potential weld defects. Adhering to the Best Practices for Operating Welding Machines on Job Sites ensures that all components, including the electric arc welder and accessories, maintain optimal performance.
Proper organization of tools also plays a significant role in jobsite safety. Accessories like clamps, magnets, and proper PPE for welders serve to secure metal parts and provide protection against hazards. Ensuring that weld joints are properly supported with the right accessories helps mitigate weld circuit issues and promotes better outcomes. Investing in the right additional tools not only improves efficiency but also enhances the quality of the final product, reducing the likelihood of defects.
Safety Protocols in Welding Operations
Effective safety protocols in welding operations are essential to ensure a secure working environment on job sites. Adhering to current safety practices helps in minimizing risks associated with sparks and other potential hazards. The implementation of robust safety systems, including thorough training and proper use of protective equipment, significantly enhances employee safety. Regular inspections and maintenance of machines, along with diligent oversight of weld cables, contribute to maintaining jobsite safety records. Incorporating the Best Practices for Operating Welding Machines on Job Sites ensures all personnel are well-informed about safety procedures and the importance of proactive measures to manage risks effectively.
Fire Hazards and Prevention Measures
Welding operations inherently involve risks, particularly concerning fire hazards. Hot metal and sparks generated during the fabrication process can ignite flammable materials in the work area. Adhering to best practices for operating welding machines on job sites is essential in minimizing these risks. Maintaining several safety conditions, such as keeping a clean work area free of combustible materials and properly securing equipment, significantly contributes to reducing the likelihood of an incident. Lever contractors also play a crucial role in ensuring that all equipment is in optimal condition to prevent equipment failure that may lead to catastrophic events.
Implementing design safety measures is equally important for occupational safety. Welders must be aware of specific metal fume characteristics that may pose additional fire risks. Safety tips, such as ensuring the presence of fire extinguishers and maintaining an emergency response plan, are vital elements to include in the overall safety strategy. By focusing on practice safety principles, welders can create a safer work environment, fostering both productivity and protection against fire hazards in welding operations.
Emergency Response Plans for Welding Incidents
Effective emergency response plans are crucial for maintaining overall safety records on construction sites. These plans should focus on the specific risks associated with welding operations, such as the potential for injury from electrical equipment or fire hazards. By having the right equipment available and clearly defined procedures in place, contractors can minimize worker downtime and ensure that everyone knows how to respond to welding incidents. Incorporating Best Practices for Operating Welding Machines on Job Sites into these emergency plans strengthens preparedness and enhances the safety culture on active job sites.
Regular training and drills should be part of emergency response protocols to ensure that all personnel are familiar with the procedures related to welding incidents. Shop equipment, including fire extinguishers and first aid kits, must be easily accessible and in working condition. Proper documentation detailing safety standards, potential risks, and steps for repair should be readily available for all workers. By emphasizing these elements in emergency response planning, contractors can create a safer work environment, ultimately reducing the likelihood of serious incidents during welding operations.
Environmental Considerations for Welding
Welding operations in the construction industry must prioritize environmental considerations to ensure a safe and healthy job site. Best Practices for Operating Welding Machines on Job Sites involve selecting newer equipment that adheres to industry-standard technology, which can significantly reduce harmful emissions compared to conventional equipment. Workers should always follow manufacturer instructions and safety guidelines to mitigate the risk of jobsite accidents. Properly managing fumes and air quality becomes crucial, especially in confined spaces, where exposure to toxic substances can pose serious health risks. Adopting universal safety standards not only safeguards workers but also promotes a sustainable approach to using construction materials effectively. Emphasizing these practices contributes to a safer working environment while maintaining compliance with environmental regulations.
Best Practice | Description | Benefits |
---|---|---|
Equipment Selection | Choose newer welding machines that meet environmental standards. | Reduces harmful emissions and enhances safety. |
Fume Management | Implement effective fume extraction systems in confined spaces. | Improves air quality and protects worker health. |
Training and Compliance | Conduct regular training on safety guidelines and manufacturer instructions. | Ensures adherence to safety protocols and reduces accident risks. |
Material Usage | Adopt sustainable materials and recycling practices in welding. | Promotes environmental sustainability and resource efficiency. |
Managing Fumes and Air Quality on Job Sites
Proper management of fumes and air quality on job sites is crucial for the safety and health of workers. Implementing best practices for operating welding machines on job sites includes conducting a full inspection of the area before beginning work. Workers should be mindful of hazardous coatings and byproducts generated during welding. Utilizing new equipment that is designed to minimize fume emissions can significantly reduce health risks. Safety shoes and other personal protective equipment (PPE) should be worn at all times to mitigate exposure to harmful substances.
Effective ventilation systems are essential in structural jobsites, especially for structural steel erectors working in confined spaces. These systems are designed to disperse fumes and maintain a safe air quality level. Regular maintenance of equipment, along with proper use of metal tongs to handle hot materials, can further prevent safety violations related to air quality. A thorough safety introduction at the beginning of each project ensures that all workers are aware of the risks and the measures in place to reduce them.
Conclusion
Implementing the Best Practices for Operating Welding Machines on Job Sites is essential for ensuring both productivity and safety. Understanding the nuances of equipment powered by a diesel or gasoline engine, alongside standard local power supplier connections, plays a crucial role in maintaining smooth operations. Skilled labor is necessary to navigate the complexities of welding processes while adhering to all established safety measures. Utilizing tools like a safety-type disconnecting switch can greatly reduce risks related to dirty power. These elements combined create a safer work environment, ultimately benefiting every job undertaken on-site.
FAQS
What are some best practices for successful welders when operating welding machines on construction jobsites?
Successful welders should prioritize safety by always wearing appropriate PPE for welders, ensuring welder cables are in good condition, and properly managing diesel/gasoline engine equipment. Additionally, understanding the role of welding studs in various projects can enhance the quality of their work. With proper training and a solid grasp of 36-week welding technology, welders can minimize trips and maximize efficiency while operating equipment on construction jobsites.
What precautions should welders take to avoid hazards and ensure safety while operating welding machines at job sites?
To ensure safety while operating welding machines, welders should always be mindful of potential trips that can occur due to clutter or equipment on the ground. It's essential to maintain a clean workspace to prevent accidents. Additionally, wearing appropriate PPE for welders, such as helmets, gloves, and protective clothing, is crucial to protect against sparks and heat generated during the welding process.
How can trips and hazards be minimized for welders while using welding machines in construction settings?
To minimize trips and hazards for welders while operating welding machines, it is essential to ensure that the work area is free from clutter and obstacles. Welders should always wear proper personal protective equipment (PPE) to safeguard against potential dangers. Being mindful of surroundings and keeping cables organized can further reduce the risk of trips, allowing welders to focus on safe and efficient operation.
What steps can welders take to reduce trips and utilize proper PPE while operating welding machines on job sites?
To minimize trips, welders should ensure that work areas are clean and organized, avoiding clutter and obstacles. Additionally, wearing appropriate PPE, such as slip-resistant footwear, safety glasses, and flame-resistant clothing, is crucial for welders to protect themselves while working safely with welding machines.
How can trips be prevented for welders using welding machines, and what role does PPE play in their safety on job sites?
To prevent trips for welders while operating welding machines, it's essential to keep the work area tidy and free of obstacles. Utilizing proper PPE for welders, such as helmets, gloves, and durable footwear, further enhances safety by providing protection against potential hazards encountered on job sites.
How can welders ensure their safety by minimizing trips and effectively using PPE while operating welding machines?
To ensure safety, welders should arrange their work area to minimize trips, which includes keeping cables organized and removing obstacles. Additionally, utilizing appropriate PPE, such as gloves, helmets, and protective eyewear, is crucial for welders to protect themselves from potential hazards that may arise during welding operations. Emphasizing both trips and proper PPE helps enhance the overall safety of welders on job sites.
What strategies can welders implement to address trips and enhance PPE effectiveness while using welding machines at job sites?
Welders can incorporate various strategies to reduce trips and enhance the effectiveness of PPE. Maintaining a clean workspace free from obstructions can significantly minimize trips for welders, while regularly inspecting and properly fitting PPE for welders ensures a higher level of safety and protection while operating welding machines.
What are effective ways for welders to enhance their safety and reduce trips when operating welding machines on job sites?
To enhance safety and reduce trips, welders should maintain a clean work area by regularly removing obstacles, use proper PPE to protect against potential hazards, and be aware of their surroundings at all times. Additionally, ensuring that welding machines are in good working condition and using cord management systems can prevent trips and help welders focus on their tasks safely. By implementing these best practices, trips can be minimized for welders while effectively utilizing PPE.
What strategies can help welders prevent trips and improve the effectiveness of PPE while using welding machines on job sites?
To help welders prevent trips and improve the effectiveness of PPE, it is crucial to maintain a clean and organized work area by removing any obstacles and hazards that could lead to slips. Additionally, using proper PPE such as slip-resistant footwear and ensuring all gear fits well can significantly enhance safety for welders. Regularly inspecting equipment and practicing good housekeeping can also aid in reducing trips and ensuring PPE effectiveness on job sites.
What techniques can welders employ to focus on trip prevention and ensure proper PPE usage while operating welding machines on the job site?
Welders can enhance their safety and reduce trips by implementing several techniques such as keeping the work area organized, ensuring proper storage of equipment, and being mindful of their surroundings. Additionally, the use of effective PPE, such as slip-resistant footwear and high-visibility clothing, can significantly contribute to the safety of welders on job sites by reducing risks associated with trips.
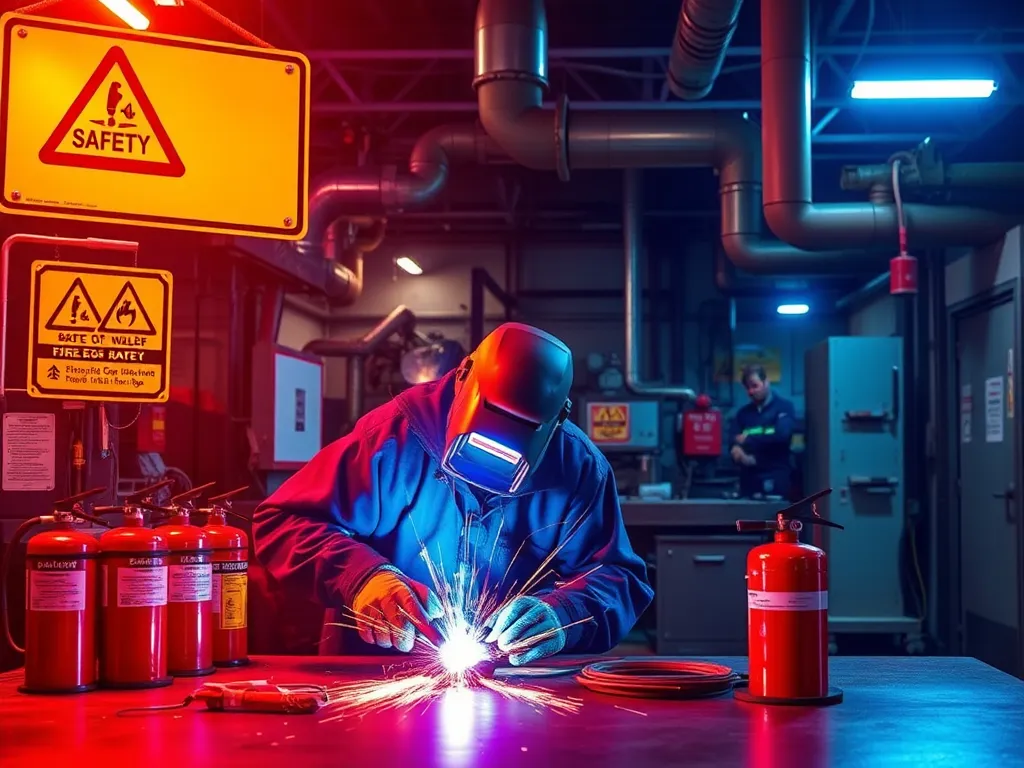
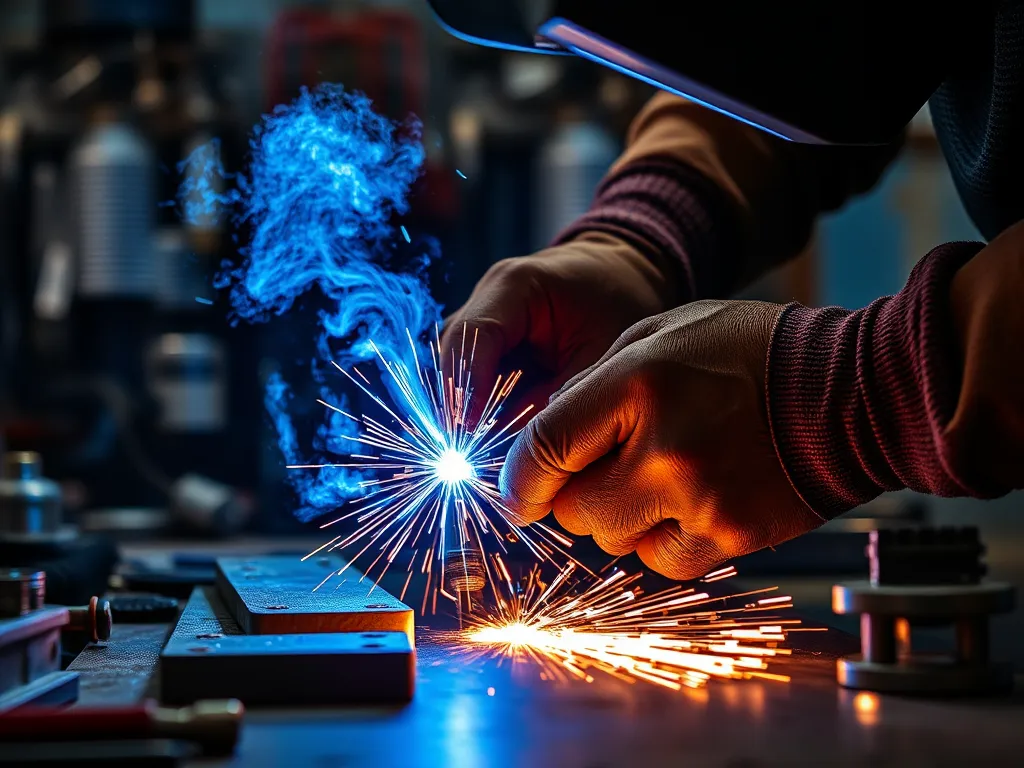
Mastering How to Tig Weld Aluminium: A Step-by-Step Guide
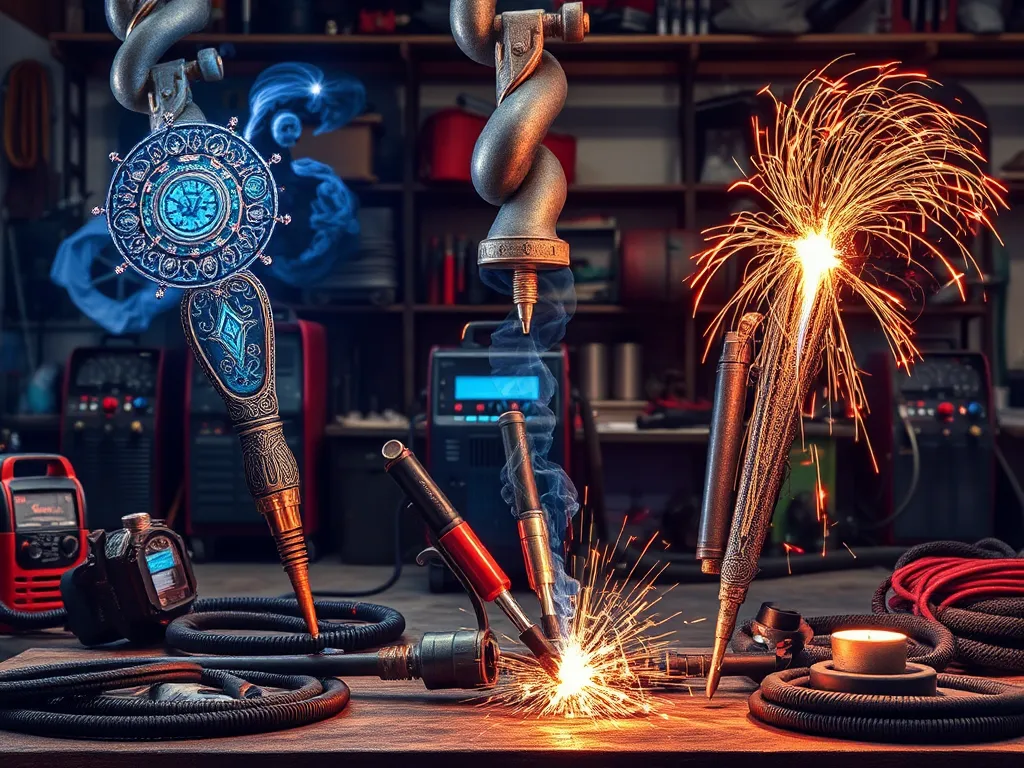
Discovering the Strongest Welding Types for Your Projects
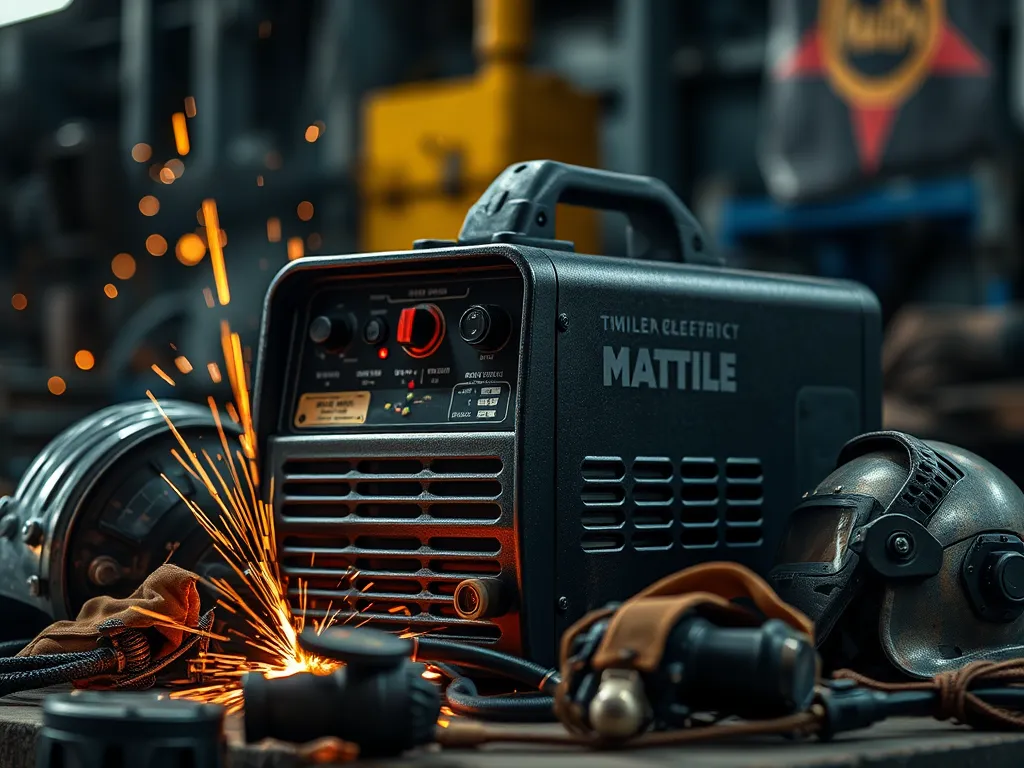